1.概述
进口红土型氧化镍矿,采用火法方式冶炼镍铁是近年来在国内广泛投资的冶金项目。在国内,目前大型镍铁冶炼企业,一般采用回转窑——矿热炉的方法,生产品位在20% 以上的镍铁。红土矿一般含镍在2%左右,以生产20%镍铁为例,镍金属的综合回收率按90% ,可知渣的产生量至少在9l%以上,渣的数量巨大,同时高温液态渣蕴含的热量非常高,合理回收渣的能量对于镍铁冶炼的成本影响很大。
2.经济效益
某镍业有限公司现有回转窑—矿热炉镍铁生产线15条,年产镍铁60万吨,每条镍铁生产线每日排渣量234t/d,按运转率85%核算,平均每天排渣量为2993.5t/d。排渣温度为1580℃,所蕴含的热量不仅数量大,且品质高,利用价值,若渣冷却温度后为130℃,其每吨显热相当于标煤78kg。如对该热量合理回收,回收率按照50% 计算,则相当于每吨渣回收热量11.455GJ,相当于每吨渣节约标煤39.08kg,每天节约标煤116.61t/d,相当于发电94.93万kWh。
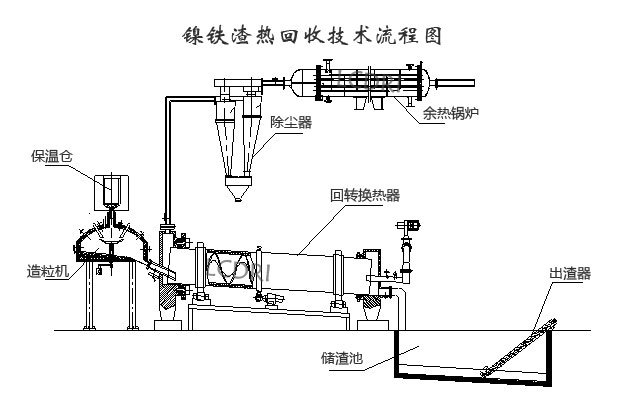
3.镍渣处理的目标
某镍业有限公司目前镍渣处理采用了熔融渣溜槽排放喷水冷却的方法,耗水量大,现场环境差,熔渣蕴含的热能没有回收。因镍渣化学成分的限制,冷却后的镍渣用于路基修筑,是性能良好的筑路材料。
因此,对镍渣处理主要应实现三个目标:一是实现无水冷却,节水并改善环境;二是冷却后的镍渣成为性能良好的筑路材料;三是实现高温熔渣热能的回收发电。
4 技术可行性
根据上述目标,就必须实现镍渣的干法粒化工艺,目前在镍铁行业没有资料表明开展了这方面的研究和应用,为此可以借助和借鉴类似行业,主要是钢铁行业相关的技术和成果。
干法冷渣即依靠高压空气实现熔融渣冷却、粒化的工艺。针对湿法处理工艺的缺点,20世纪70年代国外就已开始研究干式粒化高炉渣的方法。前苏联、英国、瑞典、德国、日本、澳大利亚等国都有研究高温熔渣(包括高炉渣、钢渣等)干式粒化技术的记录。有的方法还进行了工业试验,有影响力的主要有:滚筒法、风淬法和离心粒化法,但这些方法均没有在镍铁冶炼上应用实践。
4.1滚筒法
日本钢管公司(NKK)在福山4号高炉试验的内冷双滚筒法。两个滚筒在电动机带动下连续反向转动,带动熔渣形成薄片状粘附其上,滚筒中通入有机高沸点的流体工质,工质吸收熔渣薄片的热能后汽化,同时熔渣薄片冷却后粘附在滚筒上,形成渣片以后要由刮板清除,有机液体蒸汽经换热器冷却再次返回滚筒,回收的热量用来发电。由于渣层薄,所以传热速度很快,因此该法的热效率很高,热回收率达77%。
但滚筒法设备处理能力不高、作业率低,不适合在现场大规模连续处理冶金渣,通常只能接受来自渣罐的熔渣,同时排渣温度偏高,热回收率低,凝固的薄渣片粘在滚筒上,必须用刮板刮下来,工作效率低并使设备的热回收效率和寿命下降。
20世纪8O年代,日本的住友金属公司曾经建立了采用滚筒法处理高炉渣能力为40t/h的试验工厂。当渣流冲击到旋转着的单滚筒外表面上时被破碎化,粒化渣再落到流化床上进行热交换,可以回收50% 一6O%的熔渣显热。
单滚筒工艺的缺点在于单筒的破碎粒化能力不足,造成渣粒的粒径分布范围太,导致在流化床上与换热介质的换热面积小,换热效率低,冷却速度不足。
1995年,宝钢购买了俄罗斯乌拉尔钢铁研究院在实验室规模内研究开发的滚筒法液态钢渣处理技术。经过3年的技术转化攻关,于1998年5月在宝钢三期工程的250t转炉分厂,建成了世界上台滚筒法处理液态钢渣的工业化装置。
高温熔渣顺着溜槽倒人滚筒时,滚筒边旋转边向筒内急速喷淋,由于其内部结构特殊,不会引发爆炸,安全可靠。当高温炉渣进入简体,炉渣间分子聚合力较小,同时滚筒匀速旋转时,钢渣与内部钢球介质碰撞时被充分破碎,所以在较小能量碰撞下能将钢渣破碎成较小颗粒,其中90%颗粒的粒径在10mm 以下。应用该装置,宝钢的钢渣资源得到了综合利用,但是钢渣所蕴含的能量没有得到有效回收。
4.2风淬法
利用循环空气回收炉渣显热,通过余热锅炉以蒸汽的形式回收显热,称为风淬法。风淬法常用于处理钢渣。1977年, 日本钢管公司(NKK)和三菱重工合作研发了风淬粒化熔渣显热回收系统,并于1981年末在福山制铁所建成世界上套转炉钢渣风淬粒化热回收装置,熔渣热能回收率40~45% 。
由于钢渣自身的性质,风淬法处理钢渣不考虑粒化渣玻璃体含量的问题,而更关注热能的回收。当然,风淬法也能应用于高炉渣的处理。
新日铁、日本钢管、川崎制铁、神户制钢、住友金属和日新制钢6家公司从1982年开始在新日铁名古屋3号高炉上进行了为期6年的风淬法高炉渣干式粒化试验 ,其主要性能为:渣处理量4Ot/h,蒸汽量7t/h,蒸汽参数1.5MPa/220℃ ,热回收率65% ~79%。
风淬法的缺点也是比较明显的,由于空气的比热容比水要小,所以干燥粒化过程中动力消耗很大、与水淬相比冷却速度很慢。为了防止粒化渣在固结之前粘结到设备表面上,还必须加大设备的尺寸,从而造成设备体积庞大、复杂,加工制造困难,而且造价高。
4.3 离心粒化法
英国克凡纳金属公司(Kvaemer Metals)开发了一种转杯粒化气流化床热能回收技术。熔渣通过覆有耐火材料的流渣槽从渣沟流至转杯中心,在离心力作用下熔渣在转杯的边缘被粒化,然后渣粒在飞行中被冷却,渣粒碰到粒化器内壁时已经足够硬,不会粘到壁上,这一点因水冷壁的存在得以强化。
从装置上方排出的气流温度可达400—600℃ ,在集气罩上设有余热回收系统。离心粒化法曾经于20世纪80年代初期在英国钢铁公司Redes年产1万t的高炉上进行了为期数年的工业试验。
离心粒化法的设备简单、动力消耗小、处理能力大、适应性好、产品粒度分布范围窄。离心粒化技术的原理与目前在镍铁冶炼领域使用的镍铁粒化法十分相似,所不同的是镍铁流经圆盘撞击粒化后,落人到粒化池的水槽中,通过水将其进一步冷却,并通过水将其冲到振动筛上脱水、干燥。
根据钢铁研究总院对转杯法试验结果:当转杯转速为3000r/min,熔渣流量为2t/min时,所需要的电机功率约为12~15kW ,能耗大大低于风淬粒化。
钢铁研究总院2004年就已开始研究高炉渣急冷干式粒化技术,对离心粒化与风淬相结合的工艺也进行过相关的实验。以离心力保证粒化渣的粒度分布。风淬主要保证其降温速率以控制玻璃体含量并辅助调节粒度分布,试验结果证明该方法具有粒化效率高、动力消耗低的优点。
4.4现有技术的局限
目前高炉渣急冷干式粒化技术主要是结合钢铁行业需要开发的,其需要主要是三点:一是炉渣中含有的渣铁的回收,这一点要求熔渣粒化时粒度要尽量细碎,便于渣铁的分离回收;二是熔渣的淬冷,以使熔渣中活性矿物尽可能多的保存下来,便于资源化利用;三是熔渣中蕴热的回收利用。
基于以上三点,上述工艺用于钢铁行业内高温熔渣的干法粒化是可行的。在选择镍铁渣的干法粒化工艺时可以参考,针对高温镍铁渣冷却处理要实现的三个目标,开发适合的粒化工艺和热回收技术及装备。
5.粒化设备
借鉴钢铁行业现有干法造粒工艺的思路,结合高温镍铁渣冷却处理要实现的三个目标,其核心问题在于开发出合适的高温镍铁渣造粒设备,使其经过初步换热形成粒径合适的固态渣,进而对其进行有效的热回收。
5.1粒化设备的技术原理
从高温液态镍铁渣的物料特性出发,其液相粘度很小,流动性很好,可以像水一样流动,初始温度为1580℃,蕴含显热为2496kj/kg,其固化温度约在1100℃,高温液态镍铁渣由1580℃高液态转化为固态过程中需要放出约758kj/kg的热量,这些热量通常需要有其它媒质吸收,常用的媒质一般是水、空气及合适的固体材料等,可以采用单一或复合媒质。当采用水(25℃)、空气(25℃)作为单一冷媒时,对于每1kg1580℃的高温镍铁渣冷却到1100℃时其对应的消耗量分别为0.31kg和2.92Nm3(空气被加热到200℃)。而当采用冷态镍铁渣(130℃)作为单一冷媒时,其用量为1.30kg(假定冷渣被加热到平均500℃)。
考虑到换热速率的问题,为使高温液态镍铁渣尽量快的有液态转化到固态,就需要有效扩大与冷媒的接触面积和缩小粒径或料层厚度。考虑到物料的终利用对物料粒度的要求及设备的开发,冷却的料层厚度应保持在合适的范围内。
同时还需要考虑到高温液态镍渣在冷却固化的过程中,其粘度会随着温度的下降增加、黏附,增加脱附困难。
综上所述,干法粒化工艺过程中,需要从冷媒的选择、固化过程中物料分布状态的控制、物料与设备接触方式等方面综合考虑选择。
本方案拟采用空气冷却干法造粒工艺,并使物料与冷媒采用面接触的方式,以实现物料的冷却固化实现造粒,合理控制料层厚度,使物料与物料与空气充分接触,为热量的回收利用和镍渣的资源化利用创造条件。
获取详细方案:李工13937919268